Die Luftfahrtindustrie stellt hohe Qualitätsanforderungen an ihre Produkte und nutzt für die Qualitätssicherung die zerstörungsfreie Prüfung (ZfP). Insbesondere die Röntgenprüfung, in heutiger Zeit mehr und mehr die Digitale Radiographie/ Radioskopie (DR) und/oder immer noch die klassische Radiographie mittels Röntgenfilm, spielen eine große Rolle. Der wachsende Luftfahrtmarkt benötigt schnelle, prozesssichere Prüfungen. Viele Unternehmen steigen auf digitales Röntgen um, da hier kürzere Belichtungszeiten nötig sind, die Entwicklerchemie wegfällt, die Bewertung vereinfacht wird und der Automatisierungsgrad höher ist. Die Leistungswerte einer DR Anlage werden durch folgende Parameter beschrieben:
- Spatial Resolution (SRb):
Die Auflösung ist einer der wichtigsten Werte für die Leistungsbewertung einer Röntgenanlage. Die Ausleseelektronik der Digitalen Detektoren (DDA (Digital Detector Array), Matrixdetektor oder auch Flatpaneldetektor) bestimmt die Pixelgröße. Moderne Detektoren haben Pixelgrößen von 25 – 200 µm. Die Dicke und Art der sog. Szintillatoren (durch Röntgenstrahlung anregbare Leuchtschicht auf der Ausleseelektronik) bestimmen außerdem maßgeblich das Auflösungsvermögen von Flatpaneldetektoren. Bei dickeren Szintillatoren kommt es zu mehr Streuung innerhalb der Leuchtschicht, sodass es im schlechtesten Fall beispielsweise sein kann, dass ein Detektor mit 100µm Pixelgröße eine höhere Auflösung hat, als ein 25µm Detektor mit einer dicken Szintillatorschicht.
Gemessen wird die Auflösung mithilfe eines Doppeldrahtsteges, ein Prüfkörper mit immer kleiner werdenden Drahtpaaren, deren Vertiefung mit Hilfe eines Linienprofils gemessen wird. Es wird nach dem ersten Drahtpaar gesucht, wo die Vertiefung weniger als 20% beträgt (siehe Figure 1: Spatial Resolution Messung mit Doppeldrahtsteg). Die zugehörige Auflösung kann dann aus einer Tabelle abgelesen werden.
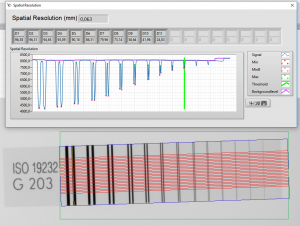
Figur 1: Spatial Resolution Messung mit Doppeldrahtsteg
- Kontrast Rausch Verhältnis (CNR):
Der Kontrast im Röntgenbild kann mittels Drahtprüfkörpern oder Lochprüfkörpern bestimmt werden. Im Luftfahrtbereich haben sich Lochprüfkörper nach ASTM E1742/E1025 durchgesetzt. Diese Prüfkörper haben eine definierte Dicke und 3 Löcher, wo der Durchmesser der Löcher jeweils das Einfache (1T), Zweifache (2T) und Vierfache (4T) der Prüfkörperdicke entspricht. Entsprechend der Dicke des durchstrahlten Bauteils, wird der entsprechende Prüfkörper ausgewählt und der mittlere Grauwert des 4T Loches wird vom mittleren Grauwert auf dem Prüfkörper (IQI) subtrahiert und durch die Standardabweichung dividiert (siehe Figure 2: CNR Messung im 4T Loch).
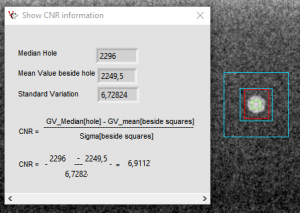
Figur 2: CNR Messung im 4T Loch
Der resultierende Wert muss mindestens 2.5 betragen um ein ausreichend kontrastierendes Bild zu erhalten. Aus diesem Wert lässt sich zusätzlich die Kontrastempfindlichkeit (CS) berechnen.
- Signal Rausch Verhältnis (SNR):
Das Signal Rausch Verhältnis beschreibt den Abstand des Störsignals zum Nutzsignal. Das SNR wird aus dem mittleren Grauwert dividiert durch die Standardabweichung in einem homogenen definierten Bereich errechnet. Dieser Wert ergibt mit einem Faktor für die erreichte Auflösung das normierte Signal Rausch Verhältnis (SNRn). Höhere SNR Werte erlauben eine größere Sichtbarkeit von Fehlern und die Bilder sind sichtbar glatter. Das SNR lässt sich am einfachsten über eine Erhöhung der Bildintegrationen verbessern.
Nach Auswahl der passenden Röntgenröhren Detektorkombination für die vorliegende Applikation ist es für die Luftfahrt unerlässlich, dass die zu Beginn erreichten Leistungswerte weiterhin dauerhaft erreicht werden. Dies muss täglich oder sogar vor jeder Schicht überprüft werden. Aus diesem Grunde wird mit sog. Prüfphantomen gearbeitet. Es gibt verschiedene Arten von Phantomen:
- Duplex Plate Phantom nach ASTM E2737: Dies ist ein zweistufiges Phantom, eine Platte entspricht der dünnsten zu prüfenden Dicke, die andere Platte entspricht der dicksten zu prüfenden Dicke. Darauf platziert sind ein Doppeldrahtsteg und die zwei passenden Lochprüfkörper nach ASTM. Die Prüfparameter (kV/mA, Brennfleckgröße, Vorfilterung, geometrische Vergrößerung, Detektormodus, Anzahl Bildintegrationen, Belichtungszeit) sollten die der späteren Prüfung entsprechen. Dieses Phantom kann individuell nach den Bedürfnissen (Größe, Dicke und Material) gefertigt werden.
- 5-Groove-Wedge nach ASTM E2737: Dies ist ein standardisierter Prüfkörper. Es gibt diesen in 2 Versionen: Heavy Metal oder Light Metal. Anhand der eingefrästen Rillen lassen sich für die unterschiedlichen Dicken, die Auflösung und die Kontrastempfindlichkeit bestimmen.
- TAM Phantom: Dies ist ein speziell angefertigtes Phantom und deckt die Prüfung von Titan- und Inconelbauteilen bis ¼ Inch ab. Auf Stufen von 0,05 bis 0,25 Inch liegen die entsprechenden Prüfkörper nach TAM ASTM E1742. Die Auflösung wird über zwei Doppeldrahtstege bestimmt.
Durch die Verwendung von CNC gesteuerten Anlagen, wie XRH222, XRH111 oder XRH Gantry, können diese täglichen Bildgütetests komplett automatisiert werden. Mit Hilfe der Image Quality Evaluation Toolbox lassen sich immer wiederkehrende Prüfungen automatisieren. Werte wie CNR, SNRn, SR, SL (Signal Level), CS lassen sich so mit einem Klick generieren (siehe Figure 3: Image Quality Evaluation Toolbox mit Duplex Plate Phantom) und als Report abspeichern.
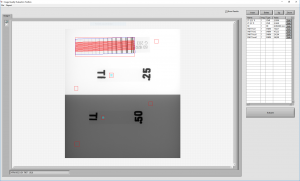
Figur 3: Image Quality Evaluation Toolbox mit Duplex Plate Phantom
Auch für die Detektorkalibrierung gibt es spezielle Anforderungen. Mit jedem Flatpaneldetektor muss eine Dunkelbildkalibrierung und eine Weißbildkalibrierung durchgeführt werden. Zusätzlich dazu gibt es sog. Bad Pixel auf dem Detektor. Eine Klassifizierung der Bad Pixel ist in ASTM E2597 angegeben und außerdem gibt es einen genormten Ablauf, diese zu identifizieren und klassifizieren, wobei eine Häufung von Bad Pixeln dazu führen kann, dass der Detektor ausgetauscht werden muss bzw. in dem Bereich keine Auswertung mehr stattfinden darf.
Auch hier bietet das Xplus++ mit der Verwendung des ASTM E2597 Dead Pixel Detection Tools ein einfaches Werkzeug um nach einmaliger Parameterfindung mit einem Klick Bad Pixel zu detektieren und klassifizieren und auch einen Report hierüber zu erstellen (siehe Figure 4: ASTM E2597 Dead Pixel Detection).
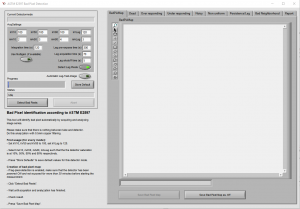
Figur 4: ASTM E2597 Dead Pixel Detection
Bei der Speicherung der digitalen Bilder wird auf einen Standard zurückgegriffen, der ursprünglich für die Medizin entwickelt wurde. Bei DICOM (oder für die Industrie DICONDE) Bildern werden neben dem unkomprimierten Röntgenbild auch Prozessdaten mitgespeichert, die mit einem DICOM/DICONDE kompatiblen Bildbetrachter wieder angezeigt werden können.