Förderprojekte
Battery-Attest.
Die röntgenbasierte Computertomografie (CT) ist eine etablierte Methode im Bereich der zerstörungsfreien Materialprüfung für die Qualitätssicherung, um verschiedene Fehlertypen in innenliegende Strukturen detailgetreu dreidimensional sichtbar zu machen. Im Rahmen des Projekts Batterie-Attest soll durch den Einsatz neuartiger Komponenten (Hochleistungsmikrofokusröntgenröhre, Hochgeschwindigkeitsmanipulator und hochgeschwindigkeitsfähiger Röntgendetektor) ein prototypisches, inlinefähiges CT-System für die Batteriezellfertigung realisiert werden. Gleichzeitig sollen Rekonstruktions- und Analyseverfahren für den Echtzeit-Betrieb entwickelt werden. Die Erprobung und Validierung des Demonstrators soll am Forschungsproduktionsstandort »FFB PreFab« durchgeführt werden.
Durch den Forschungsbetrieb (häufiger Material-, Design-, Spezifikationswechsel sowie häufiges Hoch- und Runterfahren der Anlagen) wird das Auftreten von Produktionsfehlern in Einzelprozessen unweigerlich forciert, sodass ein möglichst komplexes Spektrum an Fehlertypen erzeugt werden kann. In der Aggregation dieser Erkenntnisse soll zum Projektende eine valide, quantitative Vorhersage der Ausschussreduktion in einer Gigafactory durch das CT-System ermöglicht werden. Darüber hinaus soll mittels Dual-Energy-Technologie die Identifikation gängiger Kathodenmaterialien mit dem Ziel eine saubere Stoffstromtrennung für ein energie- und rohstoffeffizientes Recycling erprobt werden. In diesem Teilvorhaben soll ein funktionsfähiges Labormuster des technischen Aufbaus eines Inline-Hochgeschwindigkeits-CT-Systems inklusive der Möglichkeit der Integration in die FFB-Musterlinie entwickelt werden. Dabei soll zusätzlich wahlweise die Auswertung mit einer speziellen Einheit zu Kathodenerkennung ermöglicht werden, womit die spezielle Materialzusammensetzung der Kathode automatisch erkannt werden soll.
Das Förderprojekt ist Teil des Programms Batterie 2020 des Bundesministeriums für Bildung und Forschung: https://batterie-2020.de/
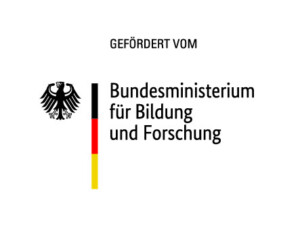
GeniAL.
Ziel des Projektes ist die Reduzierung der CO2-Emissionen, insbesondere für die Automobil- und Luftfahrtbranche, durch die Entwicklung einer effizienten Materialentwicklungsmethodik zur Qualifizierung neuer AM-Materialien am Beispiel von Aluminiumlegierungen. Es sollen neue CO2-Einsparpotentiale ermöglicht werden, indem 3D-Druck-Bauteile auch für Einsatzbereiche verfügbar gemacht werden, bei denen anwendungsspezifische Materialeigenschaften benötigt und von den derzeitigen Standards abgewichen werden muss.
Die Materialentwicklungsmethodik von GENIAL kennzeichnet sich durch eine kombinierte, digitale, smarte Entwicklung aus. Diese setzt sich aus drei Einzelschritten zusammen: der Materialanalyse mittels neuer Röntgentechnologie, der simulationsgestützten Werkstoffprüfung und der datengetriebenen, algorithmenbasierten Prozessparameter- und Legierungsgenerierung. Durch diesen vernetzten Ansatz lassen sich die Kosten um mind. 45 % und die Zeit um mind. 50 % für die Entwicklung neuer, angepasster Materialien reduzieren. Dadurch soll eine CO2-Einsparung von jährlich mindestens 4.200.000 t CO2 in einer BEV-Fahrzeugflotte erreicht werden.
Das Förderprojekt ist Teil der Förderinitiative „KMU-innovativ“ des Bundesministeriums für Bildung und Forschung: https://www.bmbf.de/bmbf/de/forschung/innovativer-mittelstand/kmu-innovativ/kmu-innovativ_node.html

RoboQuality.
In der Praxis werden große industrielle Objekte (z. B. Fahrzeugkomponenten, Batteriezellen, Flugzeugflügel) aktuell nur oberflächlich oder zerstörend geprüft. Eine tiefergehende und automatische Qualitätsprüfung solcher Komponenten ist daher nicht möglich. Roboter-CT Systeme können – in der Theorie – alle inneren und äußeren Strukturen auch solcher großen Objekte zerstörungsfrei digitalisieren. Aufgrund der Größe und Form der gemessenen Objekte sowie der kinematischen Beschränkungen der Roboter können oft jedoch nicht alle Blickwinkel erreicht werden. Für viele Anwendungen ist es daher nicht möglich, genügend Informationen für eine mathematisch korrekte und zuverlässige Digitalisierung zu generieren. Schlüsselinnovation des Projekts RoboQuality: Entwicklung und Evaluation eines Frameworks aus KI-basierten Methoden zur Generierung und Analyse aller relevanten Informationen für die Qualitätskontrolle.
Das Projekt RoboQuality wird zerstörungsfreie Qualitätskontrolle für große Objekte mit robotergestützten CT-Systemen ermöglichen und verbessern, z. B. für Automobil- und Luftfahrtkomponenten, große Gussteile und Wasserstofftanks. Durch eine Verringerung der zerstörenden Prüfung und eine Verringerung der Ausschussquote wird RoboQuality zu einer Kostenreduzierung führen, den Einsatz leichterer, aber dennoch sicherer Komponenten ermöglichen und insgesamt zu einer größeren Nachhaltigkeit führen. Um industrielle Qualitätskontrolle mit Roboter-CT-Systemen für möglichst viele Anwendungen zu ermöglichen, werden sowohl existierende 2D- als auch 3D-Fehleranalyse-Workflows durch neuartige KI-Methoden verbessert. Um sicherzustellen, dass beide Analyseansätze die anwendungsspezifisch besten verfügbaren Informationen ohne großen Aufwand für den Anwender nutzen können, wird zusätzlich Reinforcement Learning zur Trajektorienoptimierung eingesetzt.
Das Förderprojekt ist Teil des Aktionsplans KI des Bundesministeriums für Bildung und Forschung: https://www.bmbf.de/bmbf/de/forschung/digitale-wirtschaft-und-gesellschaft/kuenstliche-intelligenz/ki-aktionsplan.html

Enabl4D
Entwicklung einer robusten Bemessungsgrundlage für die Lebensdauerabschätzung additiv gefertigter Leichtbauteile in der Serienfertigung.
Ziel des Verbundprojektes ENABL4D ist die Reduzierung der CO2-Emissionen in der Luftfahrt durch die Entwicklung einer effizienten Qualitätssicherungs-Methode zur Vorhersage der Lebensdauer von 3D-Druck Bauteilen unter Belastung. So sollen neue CO2-Einsparpotentiale gehoben werden, indem 3D-Druck Bauteile auch für Anwendungen, bei denen Ermüdungseigenschaften entscheidend sind, verfügbar gemacht werden.
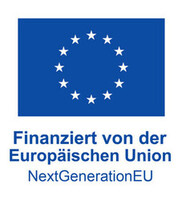
nexAMO
Teilvorhaben „Entwicklung eines kompakten CT-Systems zur Integration in ein digitales Industrie 4.0-Umfeld“ im Verbundprojekt „Entwicklung einer freiverketteten Matrixproduktion zur modularen, hochflexiblen und ressourcenschonenden Fertigung von Next-Generation-Mobility-Produkten“
Ziel des Teilvorhabens „Entwicklung eines kompakten CT-Systems zur Integration in ein digitales Industrie 4.0 Umfeld“ im Rahmen von nexAMo (Entwicklung einer freiverketteten Matrixproduktion zur modularen, hochflexiblen und ressourcenschonenden Fertigung von Next-Generation-Mobility-Produkten) ist es, einerseits ein kompaktes CT-System zu entwickeln, das vollständig in ein digitales Industrie 4.0 Umfeld integriert ist. Das CT-System muss in der Lage sein, gezielt nur bestimmte Detailregionen gemäß digitalem Auftrag zu scannen und einen Prüfreport nach digitaler Prüfspezifikation zu erstellen, der dann vollautomatisch archiviert wird. Hierzu sollen insbesondere die Protokolle DICONDE und OPC UA Anwendung finden. Zum anderen soll eine dazu passende Server-Plattform als Bild- und Messdatenspeicher entwickelt werden, die sich in die digitale Industrie 4.0-Umgebung einpasst und so die generierten Daten archivieren kann.
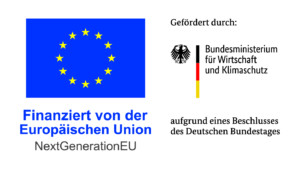
BIP Inline
Das Projekt „BatterieInspektionsPortfolio Inline“ von VisiConsult zielt darauf ab, röntgenbasierte Computertomografie-Systeme und -Lösungen zu entwickeln, welche für die Batteriezellhersteller eine zerstörungsfreie Prüfung von typischen Batteriezellarten direkt innerhalb der Linienfertigung nach der Montage ermöglichen.
Eine solche Systemintegration der Inspektion und Qualitätsprüfung bei den Batterieherstellern ist erfolgskritisch. Vor allem durch den sich beschleunigenden Markthochlauf bei der Batterieproduktion birgt diese Technologielösung hohes Potenzial. Damit dieses gehoben werden kann, besteht für ihre Entwicklung dringlicher Handlungsbedarf. Denn die Batteriehersteller müssen vorab in ihrer Produktions(stätten)planung bereits bedenken, welche Technologien ihnen in ihren Fertigungsprozessen zur Verfügung stehen.
Denn für die Qualitätsprüfung gibt es derzeit keine ZfP-Lösung, die das Problem in der Assemblierung exakt und schnell genug lösen kann. Die röntgenbasierte CT-Technologie wäre dafür prädestiniert. Für die ersten, optisch offenliegenden Produktionsschritte sind schon verschiedene Inline-Inspektionssysteme im Einsatz. Dies sind vor allem optische Bilderkennungssysteme.
Problematisch bis dato ist die Qualitätskontrolle nach dem Assembling/der Montage, wenn sich das Anoden- und Kathodenmaterial – häufig mitsamt der Elektrolyten – in der geschlossenen „Verpackung“ befindet. Hier können einfache optische Systeme nicht mehr wirken. Zu einer Prüfung kann es frühestens erneut kommen, wenn die Zelle prinzipiell schon komplett fertig ist. Mit Blick auf einen übergeordneten Kontext auch von Nachhaltigkeit, nämlich um einen möglichst langen Lebenszyklus von Batterien inkl. Recycling zu gewährleisten, wäre eine Verbesserung des Status Quo mit Hilfe der CT-Technologie „inline“ sehr sinnvoll.
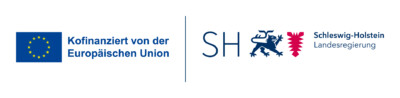