Funded Projects
Battery-Attest.
X-ray-based computed tomography (CT) is an established method in the field of non-destructive material testing for quality assurance in order to visualize various types of defects in internal structures in three-dimensional detail. As part of the Battery-Attest project, the use of innovative components (high-performance microfocus X-ray tube, high-speed manipulator and high-speed X-ray detector), a prototypical, inline-capable CT system for battery cell production is to be realized. At the same time, reconstruction and analysis methods for real-time operation are to be developed. The demonstrator is to be tested and validated at the “FFB PreFab” research production site.
The occurrence of production errors in individual processes is inevitably forced by the research operation (frequent material, design and specification changes as well as frequent system start-ups and shutdowns), so that the most complex possible spectrum of error types can be generated. By aggregating these findings, the CT system should enable a valid, quantitative prediction of scrap reduction in a gigafactory by the end of the project. In addition, the identification of common cathode materials is to be tested using dual-energy technology with the aim of clean material flow separation for energy- and raw material-efficient recycling.this sub-project aims to develop a functional laboratory model of the technical setup of an inline high-speed CT system, including the possibility of integration into the FFB sample line. In addition, the evaluation with a special unit for cathode detection is to be made possible as an option, with which the special material composition of the cathode is to be automatically recognized.
The funded project is part of Battery 2020 of the German Federal Minstry of Education and Research: https://batterie-2020.de/english/
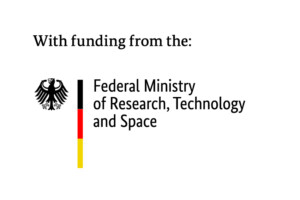
GeniAL.
The overall aim of the project is to reduce CO2 emissions, especially for the automotive and aviation industries, by developing an efficient material development methodology for the qualification of new AM materials using the example of aluminum alloys. The aim is to enable new CO2 saving potentials by making 3D printed components available for areas of application where application-specific material properties are required and deviations from current standards are necessary.
GENIAL’s material development methodology is characterized by a combined, digital, smart development. This is made up of three individual steps: Material analysis using new X-ray technology, simulation-based material testing and data-driven, algorithm-based process parameter and alloy generation. This networked approach can reduce the costs by at least 45% and the time required to develop new, adapted materials by at least 50%. The aim is to achieve annual CO2 savings of at least 4,200,000 tons of CO2 in a BEV vehicle fleet.
The funded project is part of the initiative “KMU-innovativ” by the German Federal Ministry of Education and Research: https://www.bmbf.de/bmbf/de/forschung/innovativer-mittelstand/kmu-innovativ/kmu-innovativ_node.html (German only)
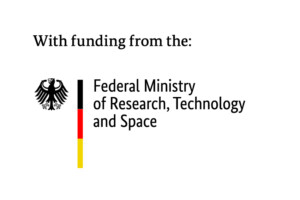
RoboQuality.
In ractice, large industrial objects (e.g. vehicle components, battery cells, aircraft wings) are currently only tested superficially or destructively. In-depth and automatic quality inspection of such components is therefore not possible. Robotic CT systems can – in theory – digitize all internal and external structures of even such large objects in a non-destructive manner. However, due to the size and shape of the measured objects and the kinematic limitations of the robots, it is often not possible to reach all viewing angles. For many applications, it is therefore not possible to generate enough information for mathematically correct and reliable digitization. Key innovation of the RoboQuality project: Development and evaluation of a framework of AI-based methods to generate and analyze all relevant information for quality control.
The RoboQuality project will enable and improve non-destructive quality control for large objects with robotic CT systems, e.g. automotive and aerospace components, large castings and hydrogen tanks. By reducing destructive testing and scrap rates, RoboQuality will reduce costs, enable the use of lighter yet safer components and lead to greater overall sustainability. To enable industrial quality control with robotic CT systems for as many applications as possible, both existing 2D and 3D defect analysis workflows will be enhanced by novel AI methods. To ensure that both analysis approaches can use the best available application-specific information without great effort for the user, reinforcement learning is also used for trajectory optimization.
The funded project is part of the action plan “AI” led by the German Federal Ministry of Education and Research:
https://www.bmbf.de/bmbf/de/forschung/digitale-wirtschaft-und-gesellschaft/kuenstliche-intelligenz/ki-aktionsplan.html (German only)
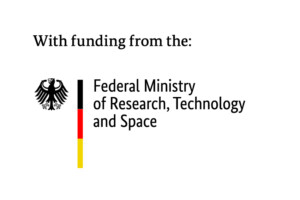
Enabl4D
Development of a robust assessment basis for estimating the service life of additively manufactured lightweight components in series production.
The aim of the joint project ENABL4D is to reduce CO2 emissions in aviation by developing an efficient quality assurance method for predicting the service life of 3D printed components under load. The goal is to leverage new CO2 savings potential by making 3D printed components available for applications in which fatigue properties are crucial.
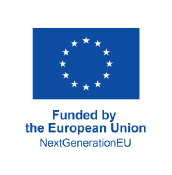
nexAMo
Sub-project “Development of a compact CT system for integration into a digital Industry 4.0 environment” in the joint project “Development of free-chain matrix production for modular, highly flexible and resource-saving production of next-generation mobility products”
The aim of the sub-project “Development of a compact CT system for integration into a digital Industry 4.0 environment” as part of nexAMo (development of free-chain matrix production for the modular, highly flexible and resource-saving manufacture of next-generation mobility products) is to develop a compact CT system that is fully integrated into a digital Industry 4.0 environment. The CT system must be able to scan only certain detailed regions according to the digital order and create an inspection report according to the digital inspection specification, which is then archived fully automatically. The DICONDE and OPC UA protocols in particular are to be used for this purpose. On the other hand, a suitable server platform is to be developed as an image and measurement data storage system that fits into the digital Industry 4.0 environment and can therefore archive the generated data.
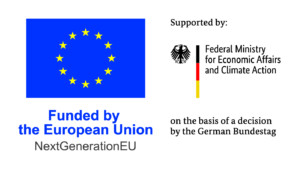
BIP Inline
VisiConsult’s “BatteryInspectionPortfolio Inline” project aims to develop X-ray-based computed tomography systems and solutions that enable battery cell manufacturers to carry out non-destructive testing of typical battery cell types directly within line production after assembly.
Such system integration of inspection and quality testing at battery manufacturers is critical to success. This technology solution has great potential, particularly due to the accelerating market ramp-up in battery production. In order to exploit this potential, there is an urgent need for action in its development. This is because battery manufacturers must consider in advance in their production (plant) planning which technologies are available to them in their production processes.
This is because there is currently no NDT solution for quality inspection that can solve the problem of assembly accurately and quickly enough. X-ray-based CT technology would be predestined for this. Various inline inspection systems are already in use for the first, optically exposed production steps. These are primarily optical image recognition systems.
Up to now, quality control after assembly has been problematic when the anode and cathode material – often together with the electrolytes – is in the closed “packaging”. Simple optical systems can no longer be effective here. The earliest a test can be carried out again is when the cell is basically complete. With a view to an overarching context of sustainability, namely to ensure the longest possible life cycle of batteries including recycling, improving the status quo with the help of CT technology “inline” would make a lot of sense.
