Welcome to VisiConsult X-ray Systems & Solutions
VisiConsult is a family-owned German global market leader in the field of customized and standard X-ray inspection solutions for non-destructive testing (NDT), quality assurance and process improvement. The VisiConsult corporate world includes the business divisions and subsidiaries VCxray, VCbattery, VCcount and VC Inspection Services as well as diondo X-ray Systems and Services with VisiConsult as majority shareholder.
Our joint goal is to provide intelligent end-to-end NDT solutions – from software via system to service – and thus, making better decisions faster. To ensure a premium quality, all products are developed and produced at local manufacturing hubs as turnkey solutions according to international standards and the German ISO 9001. More than 25 years of expertise in image processing and industrial X-ray technology, combined with experienced engineers, result in solutions that regularly set new industry standards.
VCxray
VCxray by VisiConsult serves to the broad range of industries such as aerospace & aviation, automotive, defense, energy and here in particular oil & gas as well as science & education or forensics. Naturally, we also serve the manufacturing sector with component suppliers for all these industries.
With our cutting-edge X-ray systems, our customers can get an optimum handle on additive manufacturing parts, composites, castings, electronics, pipes, tubes and tanks, plastics, turbine blades or welding, solving the challenges in non-destructive testing (NDT), quality assurance and process improvement. To ensure a premium quality, all products are developed and produced at local manufacturing hubs as turnkey solutions according to international standards and ISO 9001.
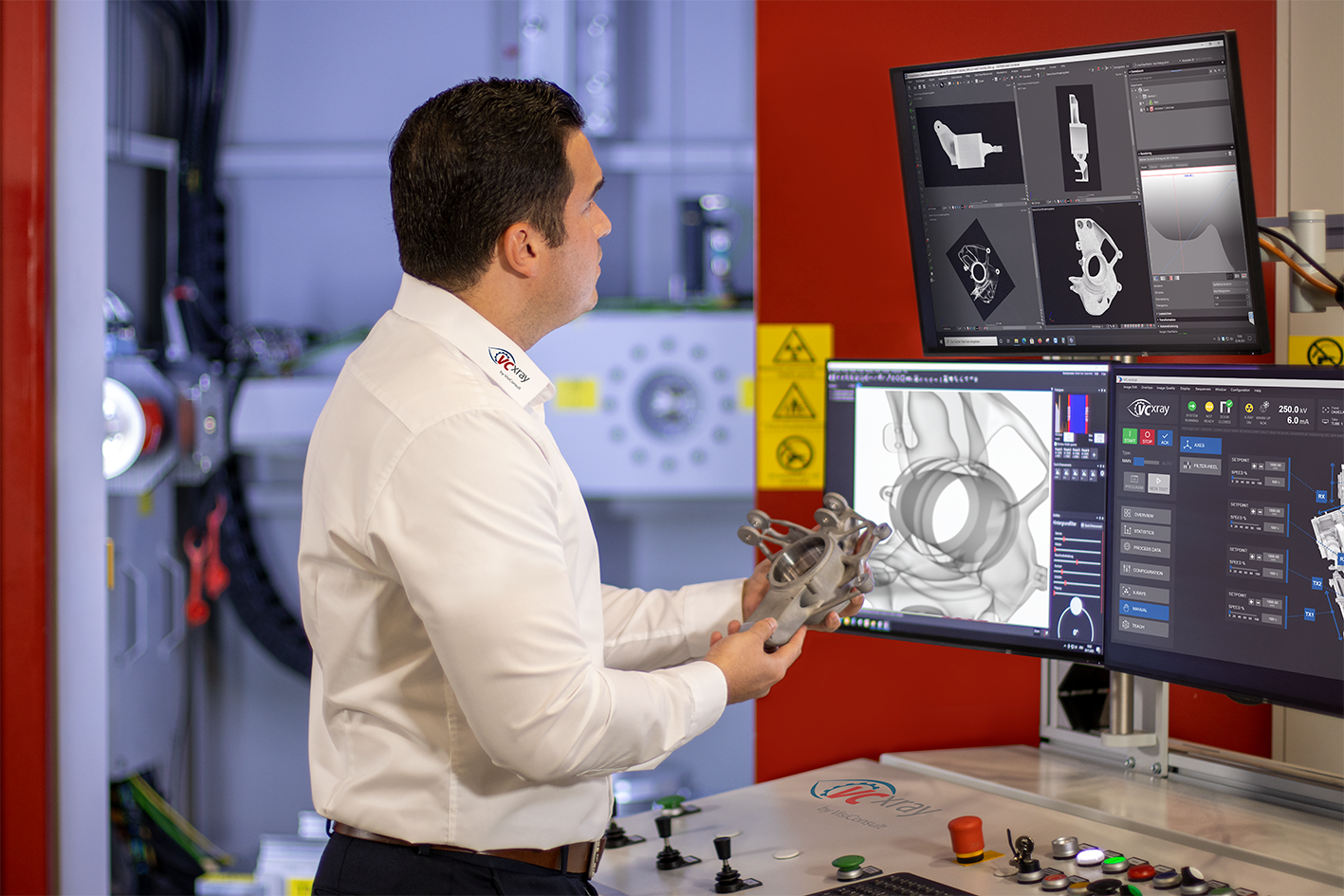
VCxray Inspection Services
VCxray Inspection Services operates as an entity in its own right worldwide, focusing on XaaS – X-ray as a Service. In doing so, customers can access VisiConsult‘s expertise and resources worldwide. With its own high-quality X-ray systems and experienced experts, VCxray Inspection Services provides its customers‘ inspection and quality managers with comprehensive and relevant information on the quality of inspected components through non-destructive testing.
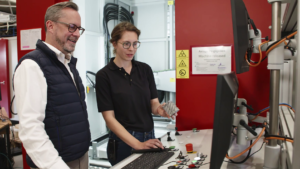
VCbattery
VCbattery by VisiConsult bundles special expertise and offers compelling 3D x-ray inspection solutions in a long-term 30% CAGR environment for the electric vehicle related market including battery cell, module and battery pack manufacturing, science and research & development, 2nd life batteries and recycling.
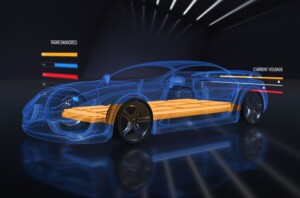
VCcount
VCcount offers electronics manufacturers an X-ray-based counting system for SMD components on reels or trays. From standalone to inline, our XRHCount system is the easiest and fastest way to revolutionize the SMD component management.
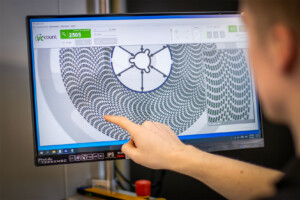
Memberships
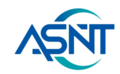
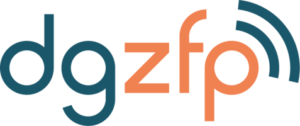
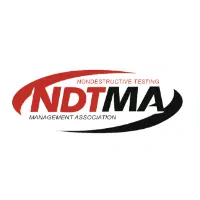
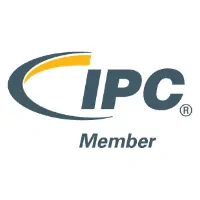
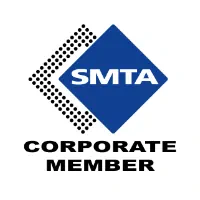
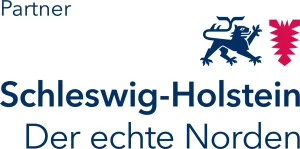
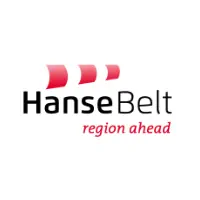
Funded projects
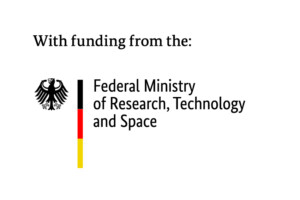
Battery Attest – part of Battery 2020.
Use of novel components (high-performance microfocus X-ray tube, high-speed manipulator and high-speed X-ray detector) and realize a prototypical inline-capable CT system for battery cell production.
Read more
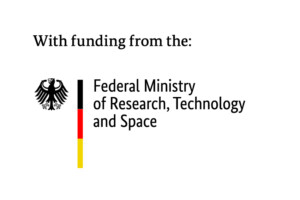
GeniAL – part of KMU-innovativ.
Development of an efficient material development methodology for the qualification of new AM materials using the example of aluminum alloys in order to reduce CO2 emissions, particularly for the automotive and aerospace industry.
Read more
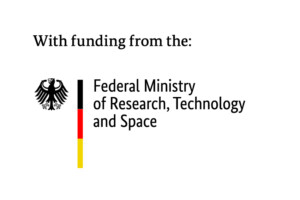
RoboQuality – part of the AI action plan.
Development and evaluation of a framework of AI-based methods to generate and analyze all relevant information for non-destructive testing and thus significantly improve it through robotic CT systems.
Read more
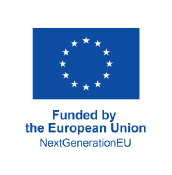
Enabl4D
Development of a robust assessment basis for estimating the service life of additively manufactured lightweight components in series production.
Read more
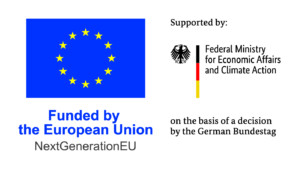
nexAMo
Sub-project “Development of a compact CT system for integration into a digital Industry 4.0 environment” in the joint project “Development of free-chain matrix production for modular, highly flexible and resource-saving production of next-generation mobility products”
Read more
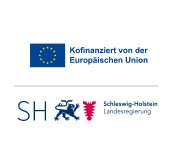
BIP Inline
VisiConsult’s “BatteryInspectionPortfolio Inline” project aims to develop X-ray-based computed tomography systems and solutions that enable battery cell manufacturers to carry out non-destructive testing of typical battery cell types directly within line production after assembly.
Read more